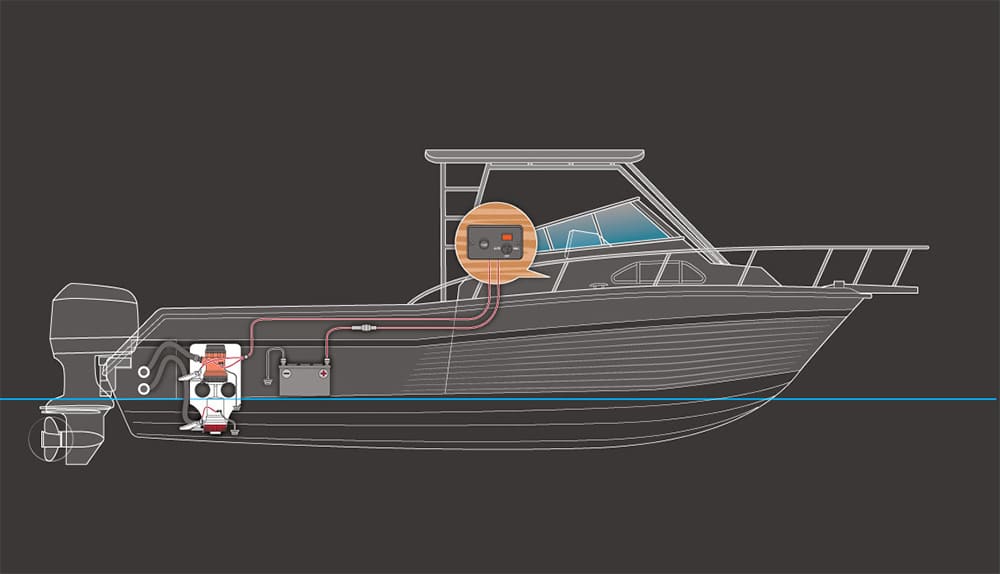
Installing the Ultimate Bilge-Pump System
A bilge pump’s massive flow rate is often touted as proof of excellence.
Pump capacity isn’t the only metric used to judge a bilge-pump system, though. For instance, smoothbore hose costs more but makes better use of pump power than corrugated hose. And the redundant safety provided by multiple pumps is hard to beat.
This project outlines the installation of a second bilge pump that’s “high and dry” until called into service. While you might choose different components, this project outlines principles I believe should be part of any “ultimate bilge-pump system.”
Getting Started
Skill Level: 3/5
Time to Complete: 4 hours
Tools and Supplies
*Nonautomatic bilge pump: Johnson 1600 ($85, westmarine.com)
*Automatic float switch: Rule Super Switch ($58, westmarine.com)
*Reinforced polyester tubing (“clear vinyl hose”): Shields Series 162 ($3.14/foot, westmarine.com)
*Three-way switch for helm control of pump
*Stainless-steel hose clamps (check with magnet)
*Through-hull fitting with 90-degree elbow
*Tie wraps
*Nut drivers, screwdrivers, drill, pliers, cutters and wrenches to suit
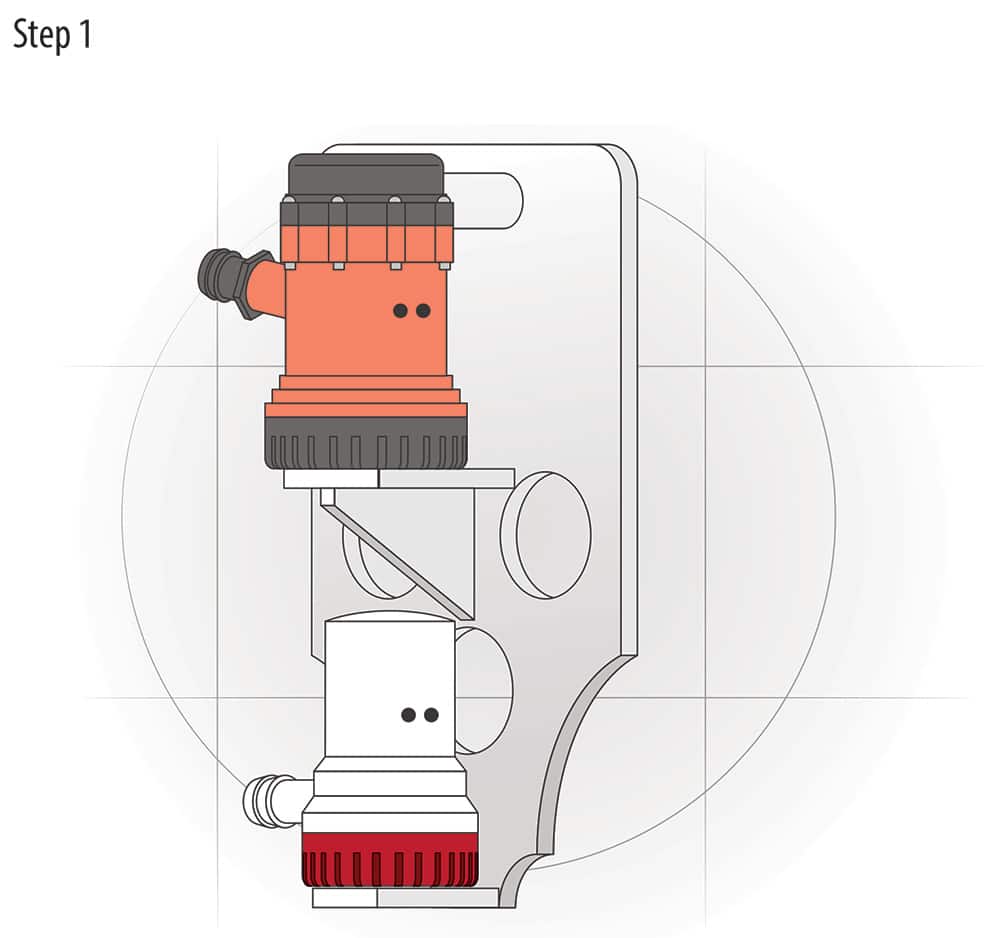
Installing the Ultimate Bilge-Pump System
1. Mount the Pump
Install the backup pump above the primary pump but below the level of the cabin sole, batteries and other critical equipment. You may need to build or buy a shelf or bulkhead-mount bracket.
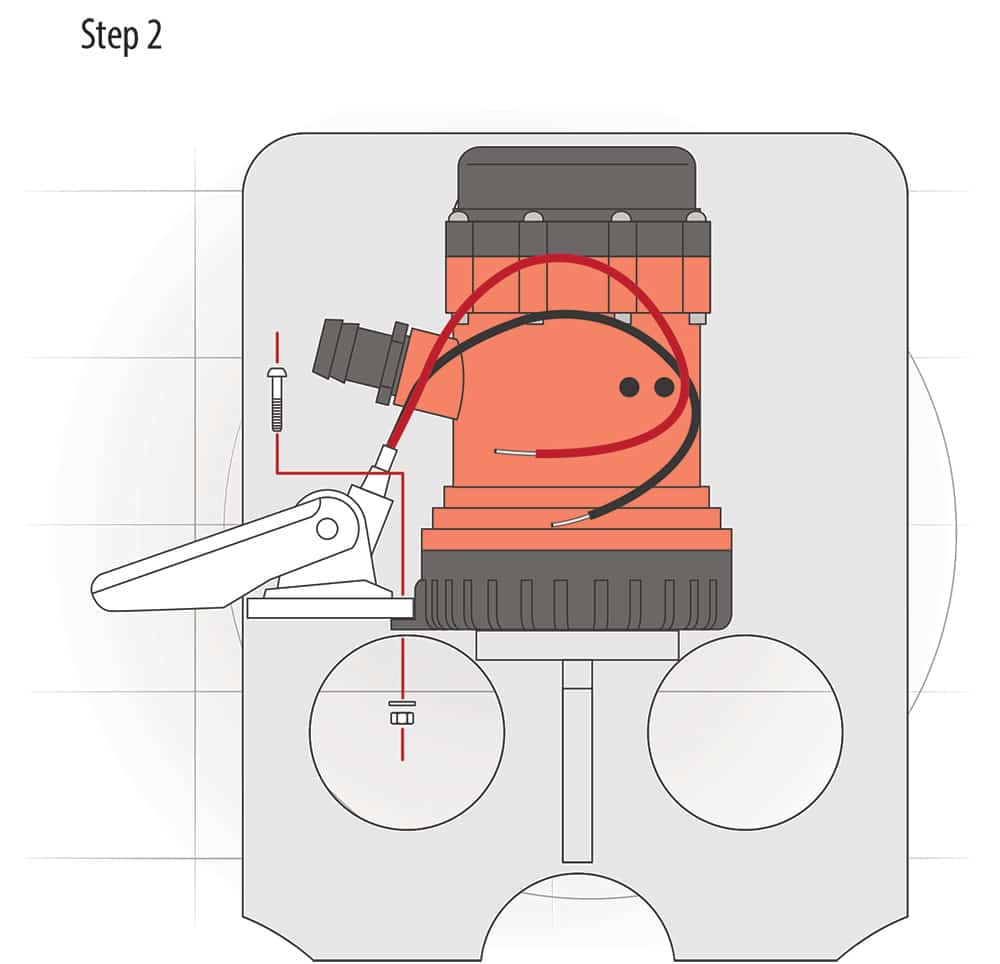
Installing the Ultimate Bilge-Pump System
2. Install the Switches
Install the automatic switch in a fore-and-aft orientation and with its hinge forward. Doing so ensures that the switch does not cycle as a result of a pitching boat or water running aft. Install a dedicated control switch at the helm. (Bilge pumps are the only appliance that may be wired directly, or “hot-wired,” to the batteries, according to the American Boat and Yacht Council.)
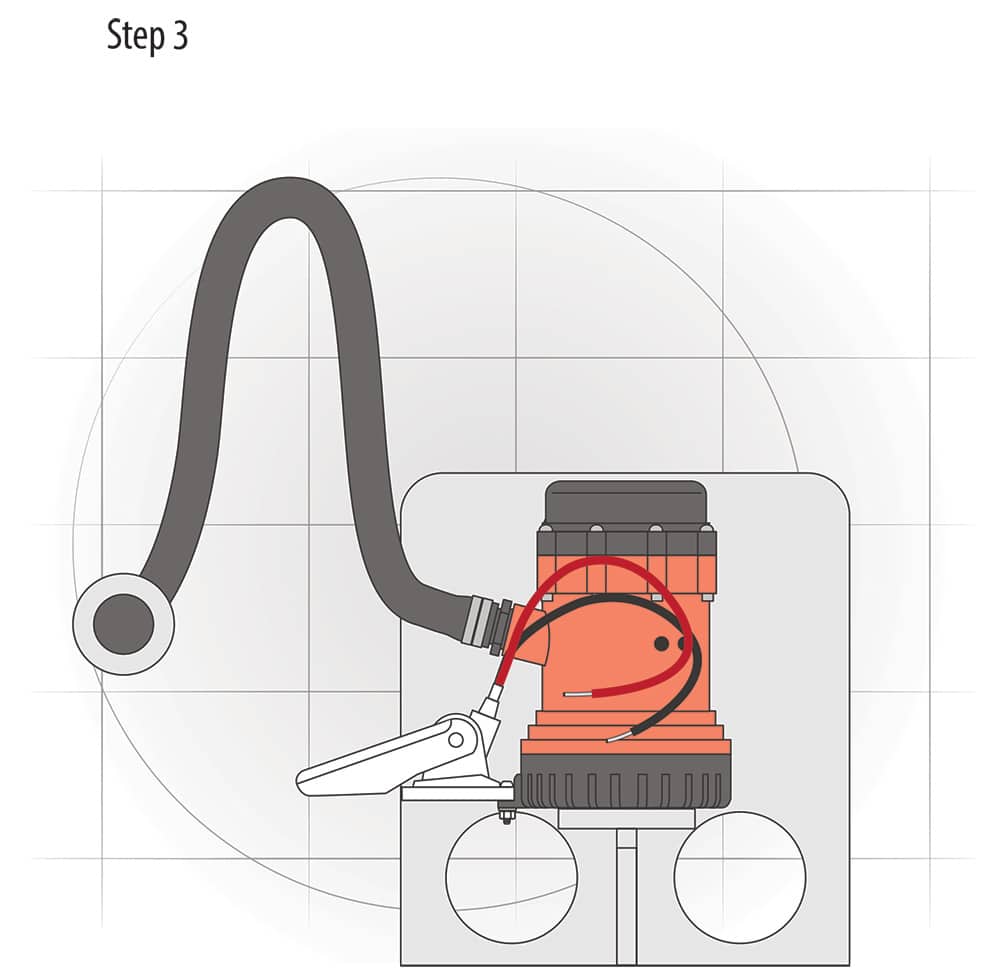
Installing the Ultimate Bilge-Pump System
3. Plumbing
Plumb hose from the pump to a point at least 12 inches above the waterline and back down to the discharge fitting, which should itself be above the waterline. Avoid kinks, bends and sags. This “riser loop” prevents siphoning. Using a 90-degree hull fitting precludes a sharp bend in the hose.
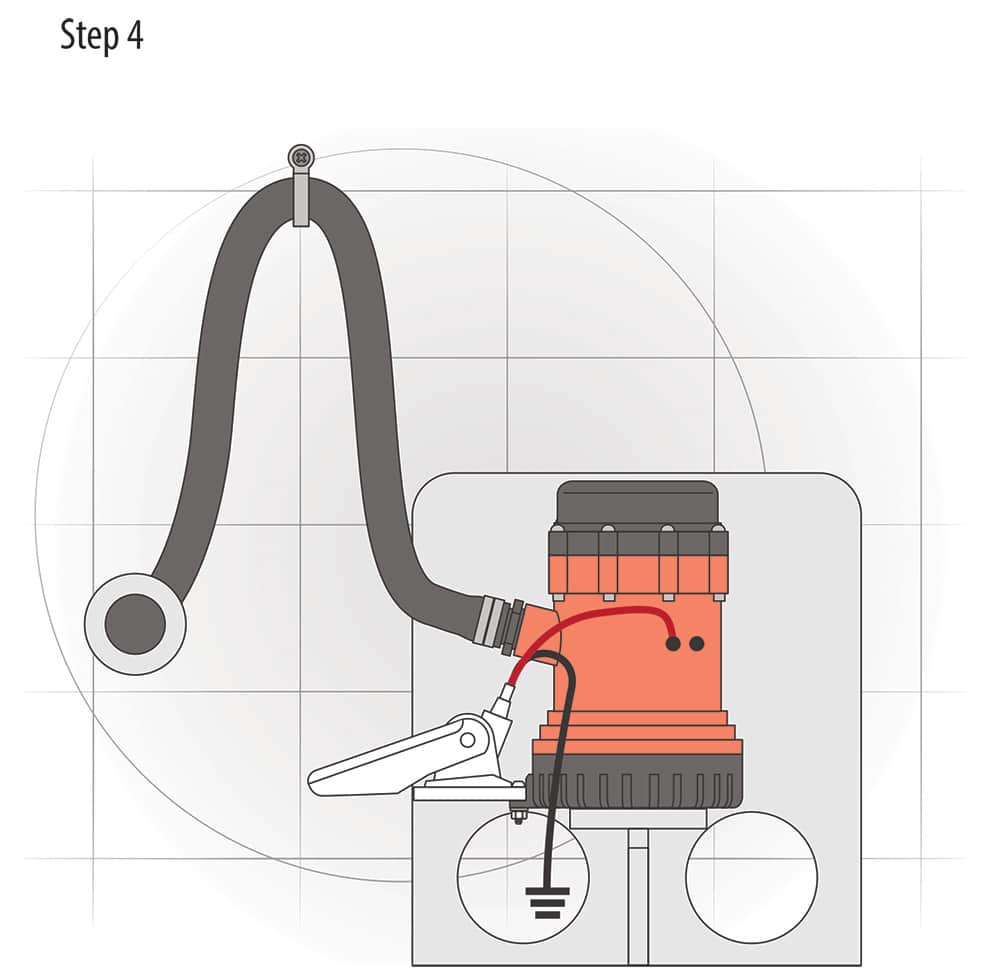
Installing the Ultimate Bilge-Pump System
4. Safe Support
Support the hose run with tie wraps, epoxy-gluing plywood to the hull side for the purpose if required. Secure the hose to fittings with clamps. Make electrical connections using best practices for waterproofing, fusing and mechanical integrity.
Quick Tip: The riser loop allows the discharge to exit lower on the hull side, reducing mess and noise from splashing bilge water.