MasterCraft has come a long way since Rob Shirley founded the company in 1968. They quickly made a mark in the watersports industry due to the luxurious performance, capabilities, and innovation of their boats. Earlier this year, we toured the MasterCraft Boats plant in Vonore, Tennessee. We witnessed the manufacturing process from start to finish. Let’s dive into how these boats are created from their unique designs to the finished product.
Innovative Design
Top notch design and engineering unlock the door to the success of any watercraft. Once a design is drafted the engineering team uses state of the art technology to create a 3D model of the boat and a detailed list of materials needed. Special software enables the team to visualize every aspect of the vessel and ensure the final product aligns with their vision. Finally the engineering team turns the design into a manufacturing plan to make sure all the materials needed and specifications line up for production.
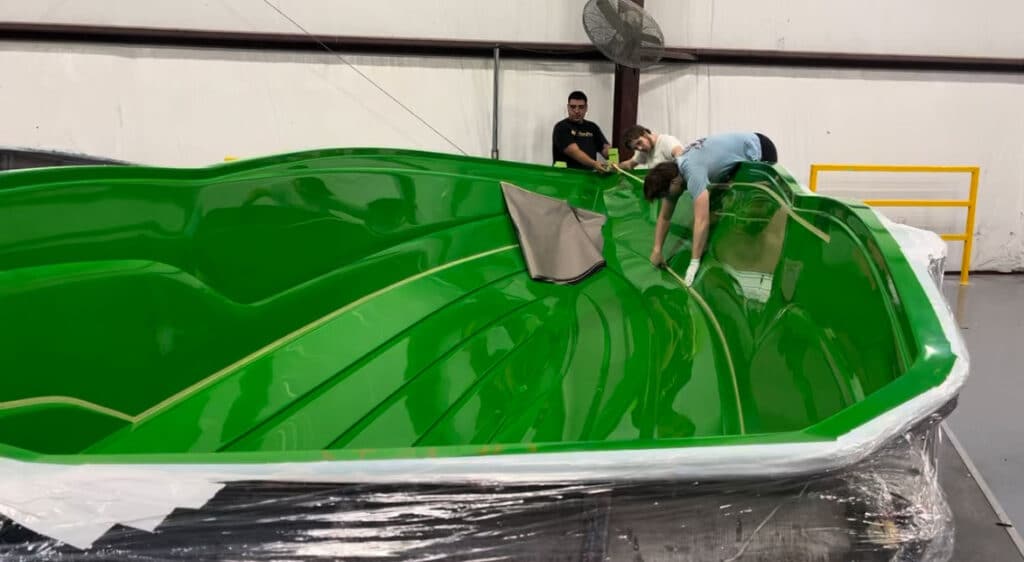
Hull and Deck Gelcoat
The foundation of the boats is a negative mold of both the hull and deck. These travel together during the manufacturing process One mark of a boatbuilder’s quality is the amount of maintenance devoted to these molds. Imperfections in a mold will appear in the finished product. MasterCraft’s molds were mirror finished on the inside. We were told their team adheres to a rigorous program of maintenance to keep them that way. Since refinishing takes time and time is money, some boatbuilders try to economize by using molds too many times before refinishing, and the results can disappoint. MasterCraft’s rigorous mold maintenance schedule helps ensure that that does not happen.
The first thing the workers do is tape-off lines to determine the design of the gelcoat pattern the customer ordered. Afterwards the molds travel to the gel spray station, where a skilled sprayer applies the gelcoat to each mold. Yes, the gel, the boat’s finish goes on first. The mold is negative remember, so parts are built from the outside in. (A special wax is applied to the mold so that the finished “part”–hull, deck, whatever–can be released when finished.)
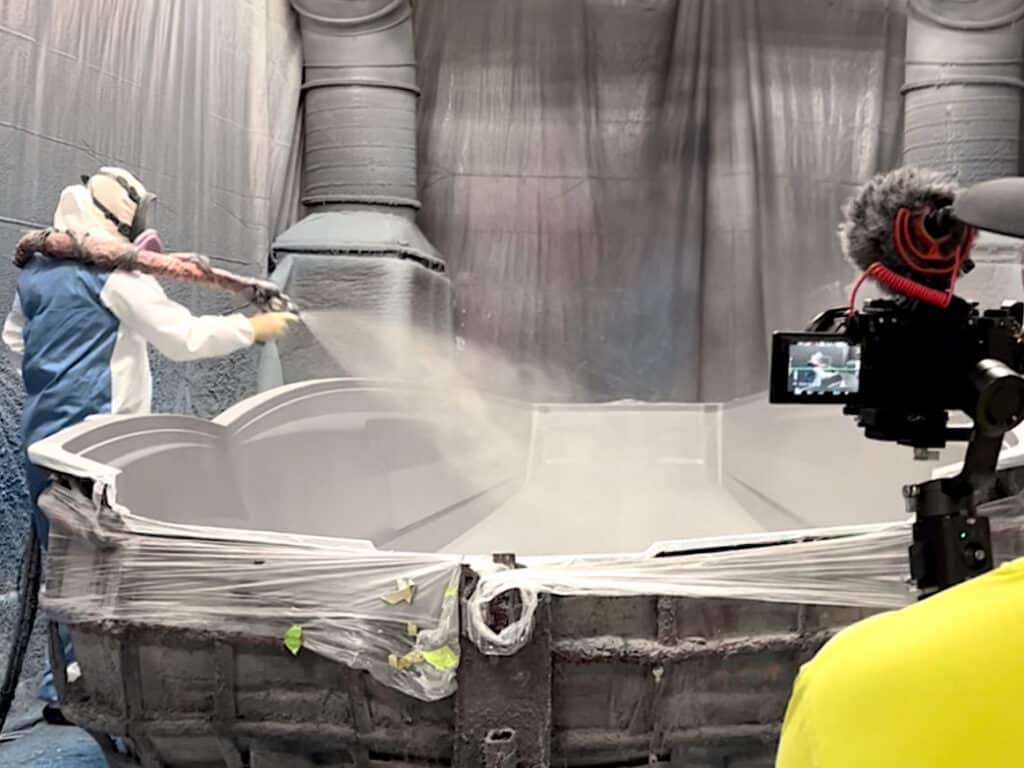
Fiberglass and Resin
Once the gelcoat has been applied to the hull and deck molds the fiberglass team begins by laying out alternating layers of fiberglass on the hull and saturating it with resin which bonds the fiberglass to the gelcoat and the other layers of glass. I watched as skilled technicians sprayed a mixture of glass and resin using what’s called chopper gun, followed by equally expert staff that applied glass mat and cloth. The resin-saturated fiberglass is “ rolled out” to remove air bubbles while ensuring complete saturation to avoid dry spots. At every stage, quality control inspectors check the quality of the work. These inspectors shine a bright light while scanning the entire part to find any air pockets or imperfections. If any are found, they are noted and a separate team makes repairs and the part is quality-checked again before the part can move on.
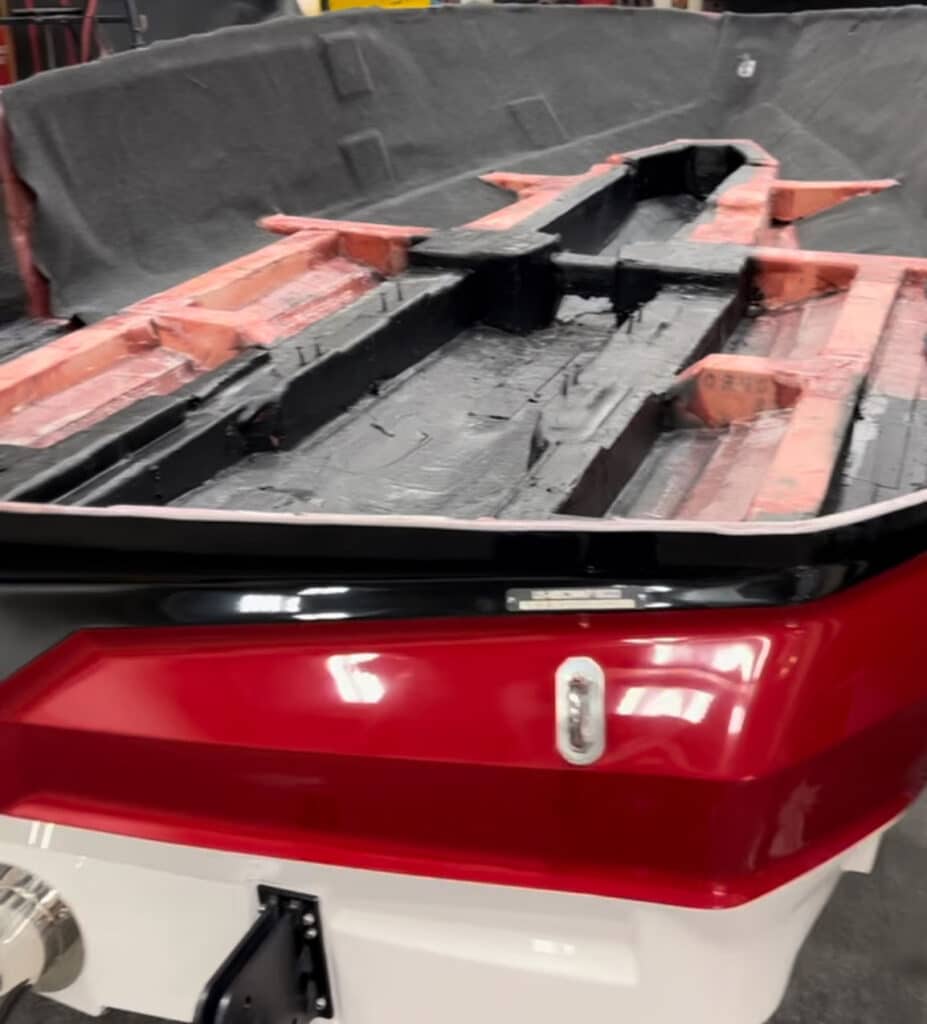
The Backbone
A stringer system made of fiberglass is inserted into the hull and runs the entire length of the boat to provide structural support for the hull. Curious what a stringer is? It’s basically the spine of the boat, consisting of longitudinal arms (the actual stringers) and members that run across the boat’s beam (called bulkheads.) The stringers provide rigidity to the hull. The stringers also help create some under deck compartments, such as the engine bay. To say the least it’s vitally important to the structural integrity of the boat that the stringer system be properly engineered and correctly installed.
An innovative feature, MasterCraft uses a lightweight, triple-density foam applied as a spacer between the hull and deck. The core provides a strong surface which acts as a vibration dampener when the boat is put together. It’s one reason creaks and groans from running are minimized while aboard a MasterCraft.
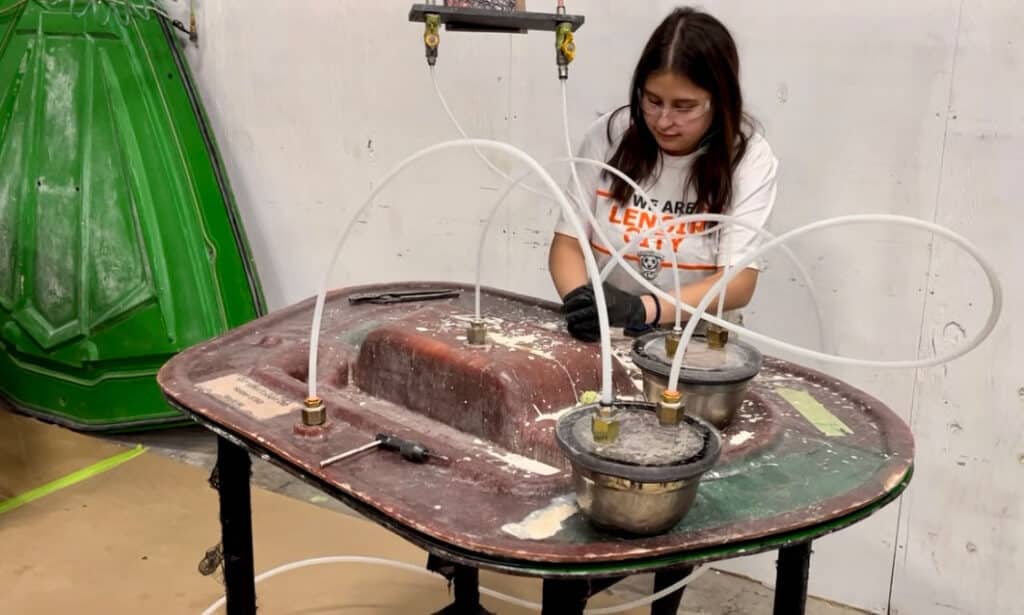
Small Parts
MasterCraft manufactures many of its small parts using a special system with two-part molds. This process is called vacuum resin infusion molding. This ensures that the resin is evenly distributed throughout the fiberglass component for the highest quality boat build. Hatch lids are one example.
To do it, a worker lays fiberglass and and resin into each of two mating molds. These are then clamped together and a vacuum is drawn. After the curing time, the molds are taken off.
This is one construction process the benefit and result of which you can actually see in the completed boat: both sides of the part are finished smooth. This looks great, makes both sides easy to wipe clean. Open a hatch lid on a MasterCraft and see for yourself.
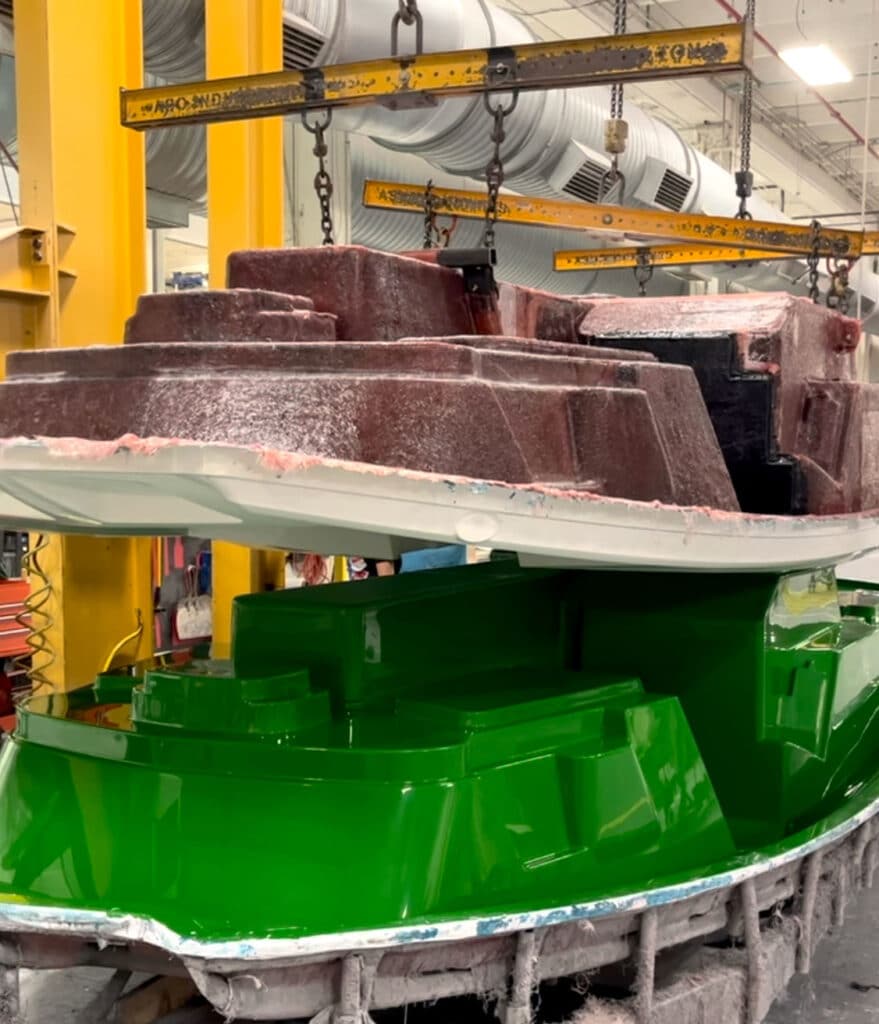
Assembly
Once deck and hull are finished, assembly begins. Workers use wedges and a hammer to begin to separate the boat’s deck from the mold, (Remember, I mentioned the special release wax that is applied before the gelcoat gets sprayed). Then, a chain lift pops it out of the mold. It’s then sent to get parts installed, such as cleats and lights and wiring. These are installed by workers while the deck is hanging overhead.
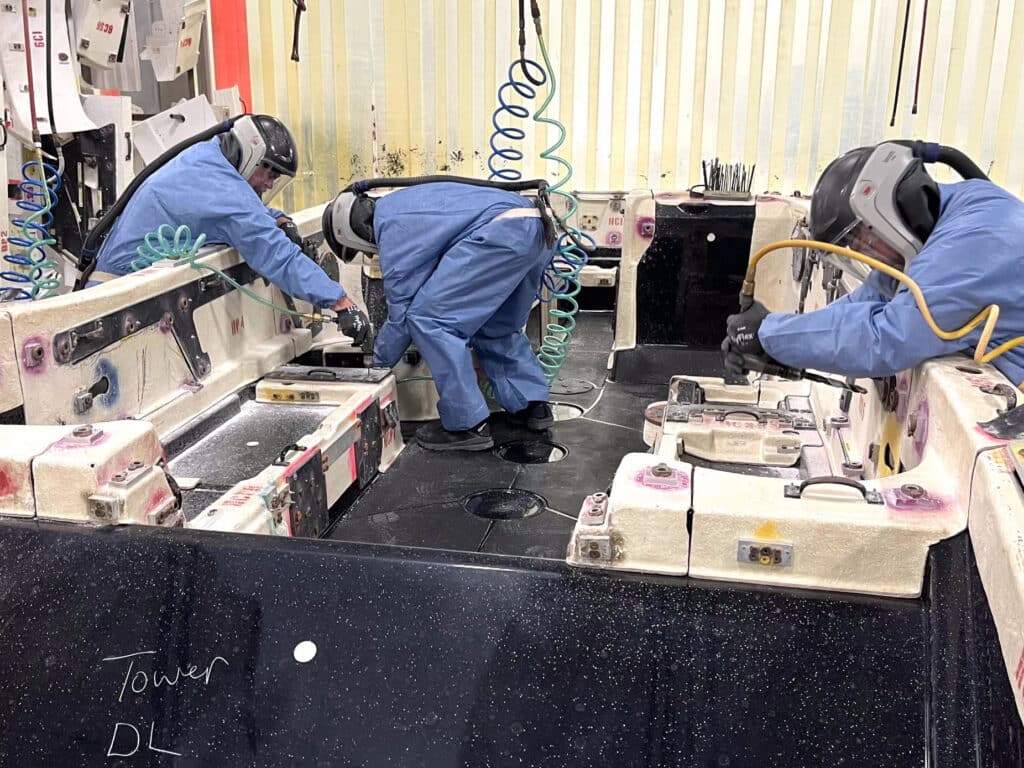
Similarly, systems are installed in the hull before it and the deck are brought together. MasterCraft workers use special templates so that holes bored for all of the wake plates and other transom fittings can be drilled with precision. The engine is installed into the boat, as is the prop shaft and rudder, along with the fuel tank, ballast tanks and all the associated plumbing.
While all this is happening, the hull and deck for a given boat are literally moving down the line beside one another. At each station, another installation process takes place.
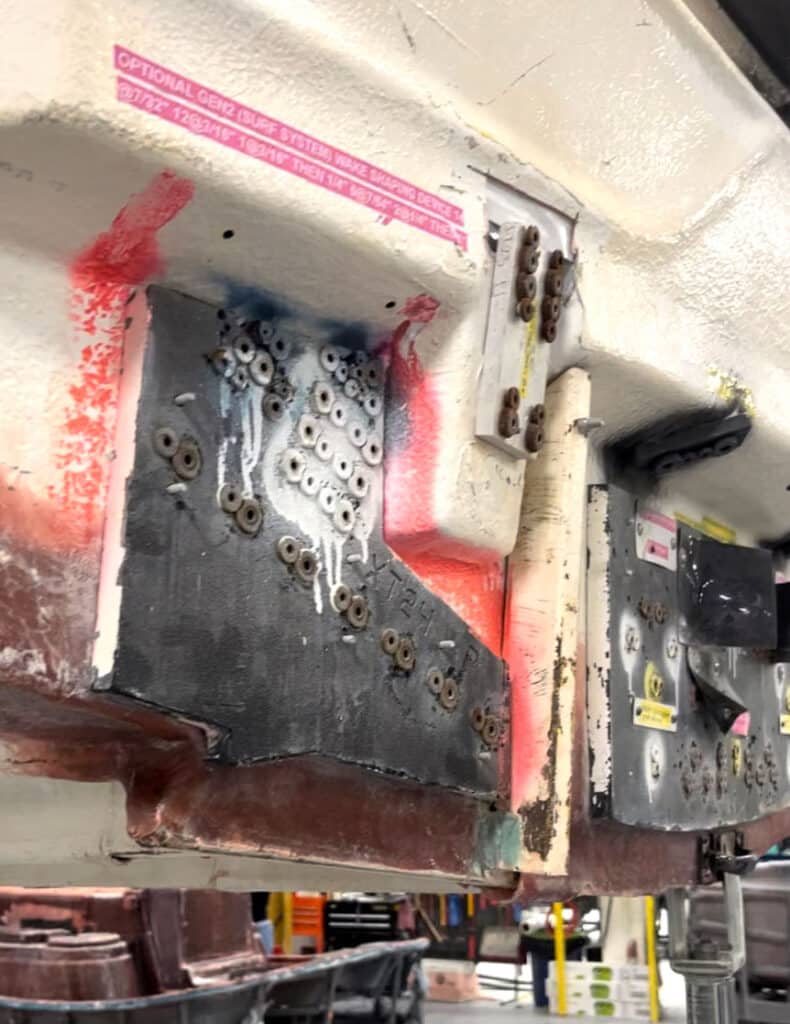
Finally, the deck is lifted above the hull and set down upon it. To be clear, the deck is the part that includes the gunwales, the inside sides of the boat and the cockpit floor, or sole. The fit is similar to a shoebox, in that a vertical edge of the deck, called a flange, overlaps a similar edge, or flange, at the top of the hull.
Sealant is applied to the hull/ deck joint before assembly. Then screws are run through both flanges. A rubrail is secured to the hull, covering this joint, and MasterCraft runs these screws through both hull and deck flanges as well. Finally, the trim piece–the center of the rubrail is installed, and its screws run through. That makes for a total of three courses of screws connecting the hull and deck of a MasterCraft, a key structural highlight that few builders copy.
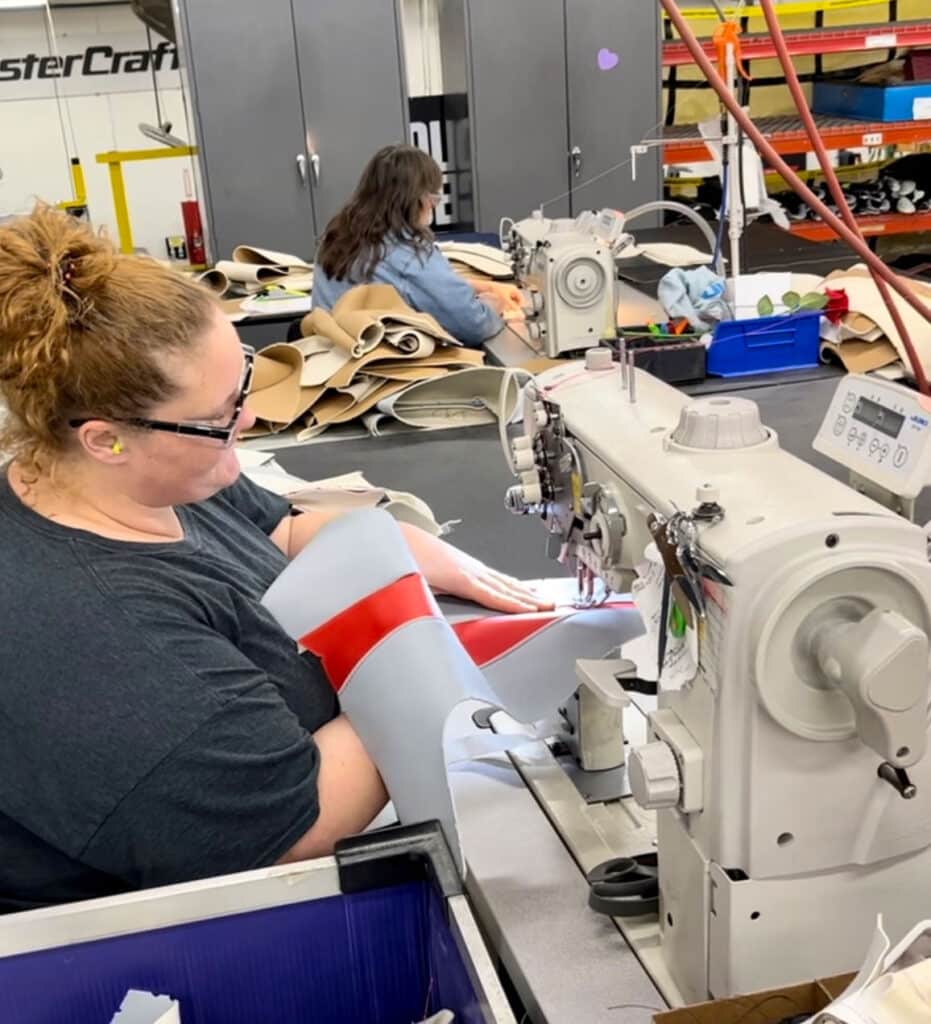
Interior
It’s at this stage that the boat’s interior such as flooring and seats are installed. It’s important to note that MasterCraft builds many components in-house, as opposed to contracting them to suppliers like some other builders. We were particularly impressed with the upholstery shop, which is staffed, we are told, by some of the boatbuilder’s longest term employees, many of whom have worked for MasterCraft for decades. While some portions of the creation of the seating and upholstery aboard a MasterCraft are automated, very much of it is hand work. So, employees with long experience prove essential for success.
It should be noted that MasterCraft offers an almost untold combination of interior designs.
Read Next: MasterCraft Boats Director of Engineering IWD Interview
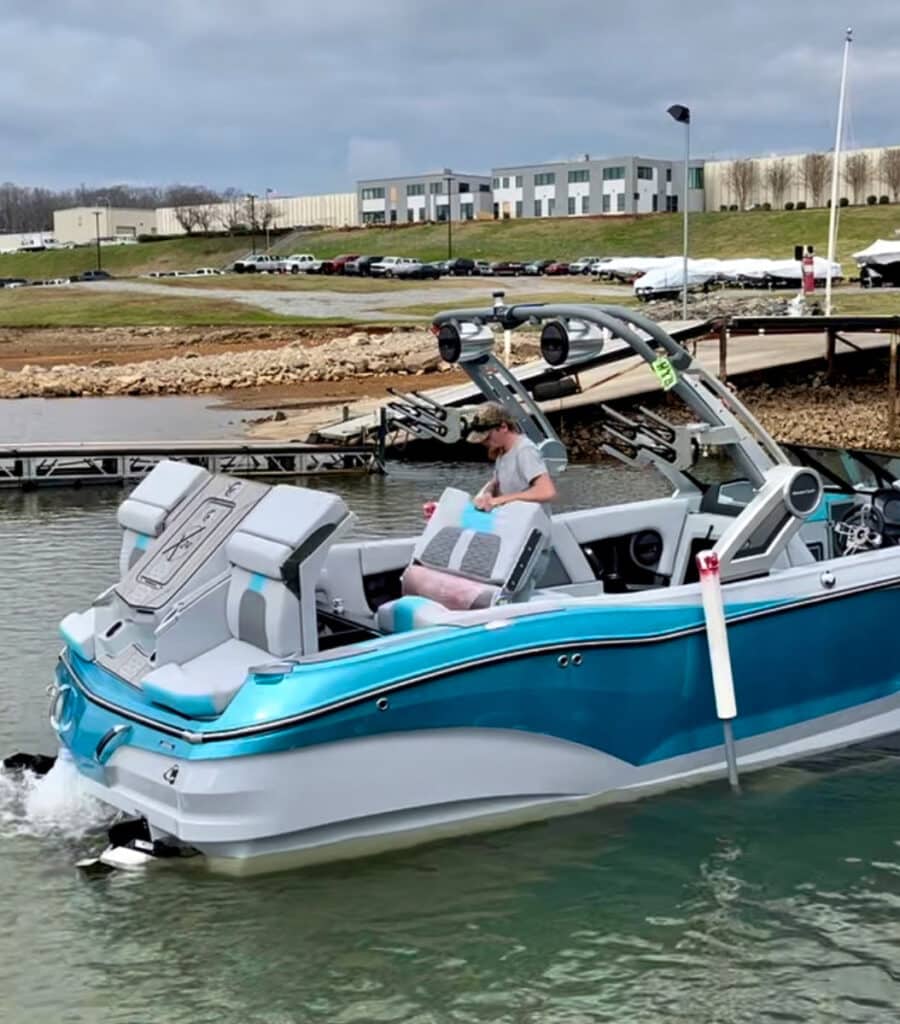
Testing and Final Finish
MasterCraft is one of the only boat manufacturers that lake tests every single boat they create before shipping to the customer or boat dealership. A MasterCraft test captain physically puts each boat through its paces out on the Tennessee River. Before you rush to file an employment application, you should know that the test crew was working hard during the raw, grey late winter day we toured the facility. Also, these captains are experts in all systems aboard.
The lake test ensures that nothing is structurally, electrically, or mechanically wrong with any aspect or part of each boat. MasterCraft’s quality control team and high standards with the added, hands-on attention of the 90-minute lake test, creates a better owner experience. Each boat then heads back into the factory right after being rigorously tested for one and a half hours on the lake.
After a MasterCraft Boat passes all quality control checks, it’s time for the final touches. The boat is then polished, buffed, and wrapped at the final finish station. Now it’s officially finished and a beautiful MasterCraft boat is sent off, ready to be placed in the hands of its new owner.
All Hands On Deck
Tour the MasterCraft Boats plant and it’s evident that its workforce is engaged and dedicated. Every employee we interacted with spoke well about their particular job’s importance to the overall finished boat. The atmosphere is one of teamwork and the plant is as well organized a boat building facility as you will find (according to our Director of Boating and Watersports, Kevin Falvey, who has toured dozens of boat plants and who accompanied me on this visit).
MasterCraft certainly uses automation and technology in the design and build of its boats. But, we were struck by something else. There is an astonishing amount of hands-on work that goes into almost every stage of the building a MasterCraft Boat. Craftsmen–boatbuilders–are required to do this. MasterCraft, we think, then, is aptly named.