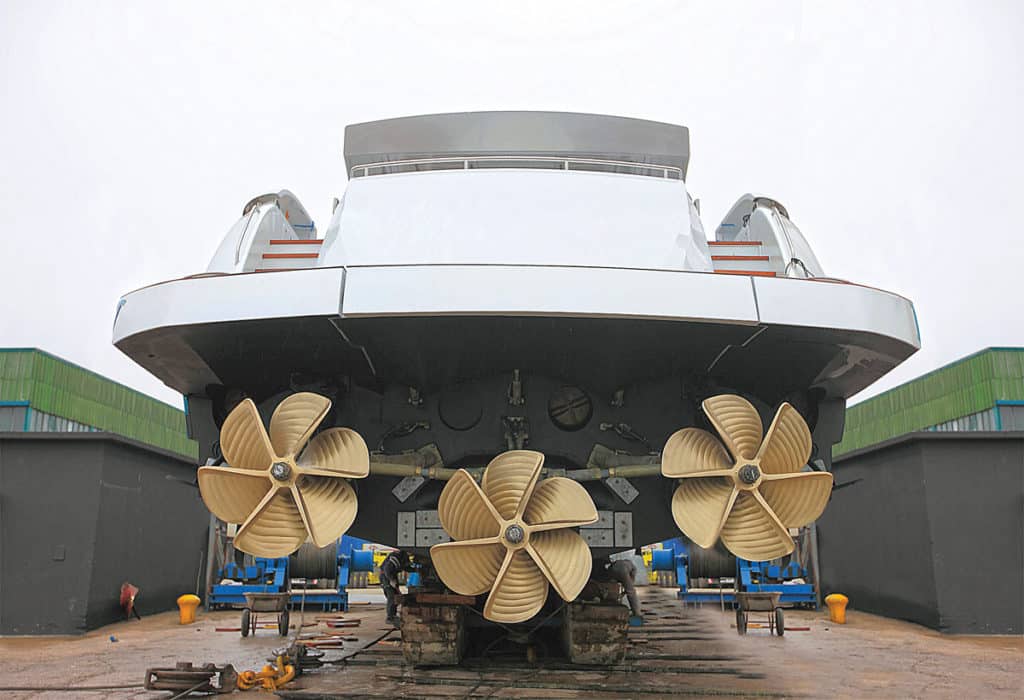
Years after the space race, propeller design remained a sea-trial-and-error endeavor: haul, tweak the props, relaunch, sea-trial, repeat. Finally, the U.S. Navy paid the Massachusetts Institute of Technology to predict propeller performance using a computer.
The resulting 3-D computer models let Navy experts alter and analyze blade skew, rake, chord length and camber to maximize ship speed while minimizing noise. After the Cold War, those Navy/MIT propeller design tools became available to the private sector and, within the past 10 years, once-top-secret designs have made it to off-the-shelf production props for inboard boats as small as 35 feet.
Will a set of high-tech props increase your boat’s speed or economy, get it on plane faster, or even make it handle better? I persuaded four prop experts to share their thoughts with Boating.
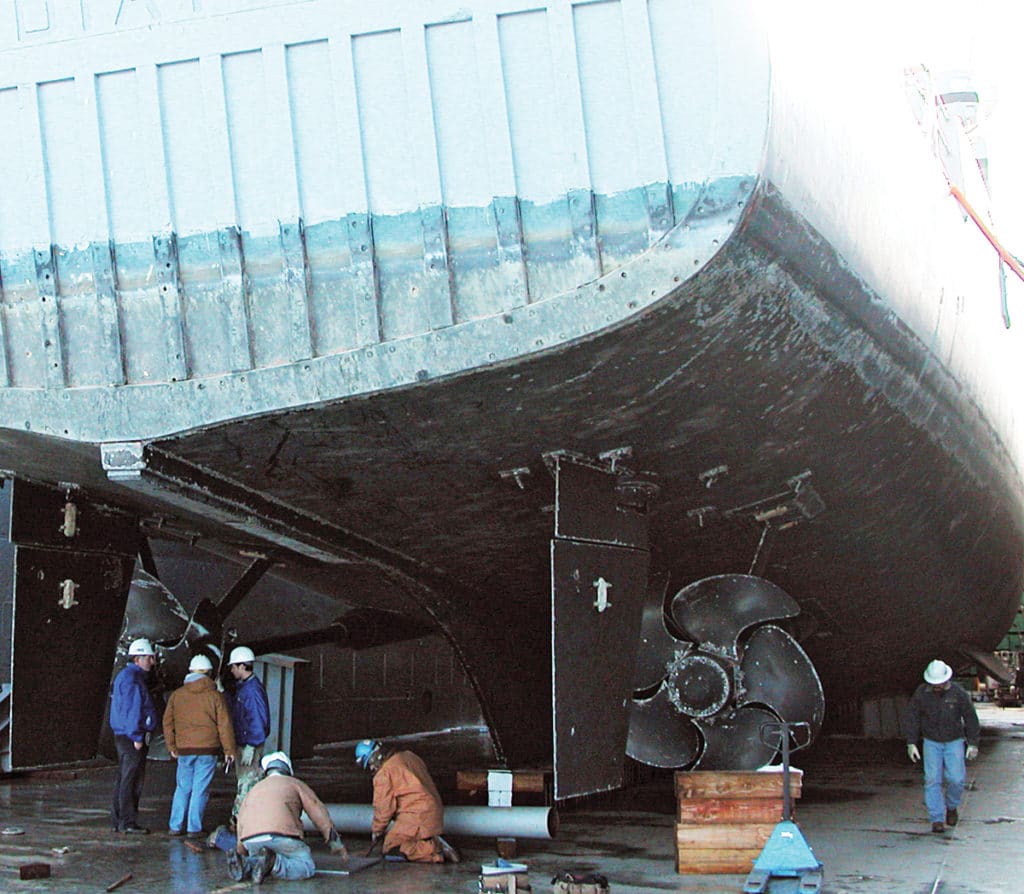
The Plane Truth
“A propeller is really just a set of rotating wings,” says Greg Platzer, who headed the surface ship propeller group for the U.S. Navy through the latter part of the Cold War. Platzer’s team curved propeller blades like airplane wings. This spread the load across the entire propeller, maximizing efficiency, minimizing cavitation and producing quieter props that were harder for enemy submarines to detect. Now a civilian, Platzer designs custom propellers for large yachts. “On yachts, we’re using the same principles for different reasons,” he says, citing props that deliver 5 to 10 percent increases in fuel efficiency and/or speed while cutting vibration by up to 75 percent.
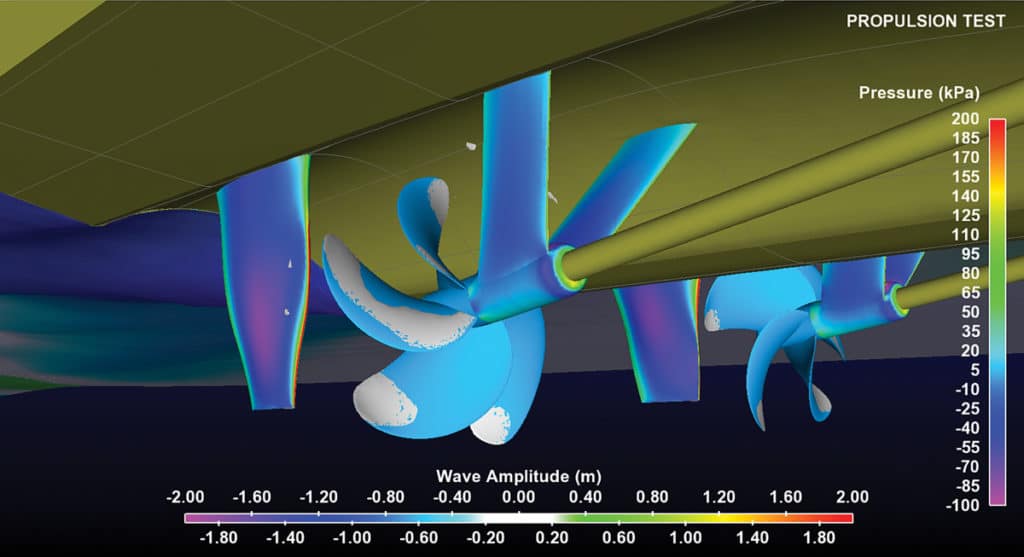
Best For Which Boats?
“A 30-knot [34.5 mph] boat that has steep shaft angles is an ideal candidate,” says Jimmie Harrison, president of Frank & Jimmie’s Propeller in Fort Lauderdale, Florida. “We’d expect to see a knot or two more speed at top end with the correct foil-shaped prop blades.”
That’s not to say new props won’t do anything for slower boats, but there are more variables. “On a boat cruising around 18 knots [20.7 mph], where it’s just on plane, the right propeller design can mean a world of difference — maybe a 5-knot [5.7 mph] gain,” says naval architect Kevin Mitchell of Michigan Wheel Marine. Mitchell says diesel-powered boats over 40 feet using at least a 2-to-1 gear reduction typically benefit most. “In gas boats, with smaller-diameter props turning close to engine rpm, the best design might be that traditional flat-faced prop with some cup on the trailing edge of the blade,” he says.
As engine horsepower increased over the past decade, ideal prop diameter for a given boat model typically increased as well. But since boatbuilders usually can’t change prop diameter on a venerable design, increased horsepower often leads to increasingly inefficient props. This holds true for boaters who have repowered as well. One solution to the conundrum comes from advanced prop design. “The optimum diameter of a five-blade propeller is always going to be smaller than a four-blade, so we gain efficiency by increasing the number of blades,” Platzer says, adding for emphasis, “With an airfoil-shaped blade, we can increase blade camber to match increased horsepower.”

Handling Benefits
Additionally, boats that benefit from lowering trim tabs considerably at cruise rpm might see big gains from foil propellers. That’s because the downward angle of propeller shafts on most inboard-powered planing powerboats helps propellers lift the stern without the added drag of lowered tabs. Airfoil-shaped blades make it easier to produce lift efficiently. Mitchell recounts an example: “A mainstream express cruiser gained 2 knots [2.3 mph] at top end, with corresponding increases in economy at cruise speed, simply by switching from our older Dyna-Quad design to our new, foil-shaped EQY propeller.”
On the other hand, “If your engines aren’t putting out enough horsepower at the rpm where the boat is coming up on plane, there probably isn’t an advantage to foil-shaped props,” Harrison says, describing the classic diesel-turbo-lag situation. “That problem is often solved with less-efficient propellers that slip more at midrange rpm.”
Plus, propeller blades raked aft increase stern lift by shifting the center of effort of that lift in relation to the fore-and-aft center of buoyancy of the boat. (Yep, inches matter at thousands of rpm.) But the reverse is also true: Blades raked forward or designed for less propeller lift might balance a boat. Often, handling problems, like a boat that tends to stuff its bow into following seas, can be mitigated.

Noise, Vibration and Cavitation
“Propeller noise, and often vibration, is primarily from cavitation,” Platzer says. “We want to unload the tips of propeller blades by changing their shape to control where on the radius of the propeller we produce thrust.” Simply adding blades alleviates noise and vibration too.

“Cavitation typically occurs as each propeller blade passes through the wake of the running gear and close to the hull,” Platzer says. With only three blades, one-third of the prop is passing through that disturbed water at any given time. Increase to five blades and only one-fifth of the prop is subjected to that added cavitation. Adding blades decreases ideal prop diameter, which increases distance between blade tips and the bottom of the boat. “The gains are linear,” Platzer says. “Doubling the tip clearance cuts noise and vibration in half.”

Skewing propeller blades — curving the edges a bit like a banana instead of leaving them symmetrical like a cloverleaf — was one of the Navy’s closest-held secrets for reducing prop noise. “That curved leading edge of the blade passes through the wake of the strut and hull over a longer arc of propeller rotation,” which spreads the effects of cavitation, Platzer says.

On boats with propeller pockets, blade tips are close to the hull over a longer arc, so new props are particularly helpful.
Trimmable Thrust
“An outboard is a blank slate,” says Steve Powers, president of PowerTech Propellers. “One engine model might be used on anything from 20 feet to 40 feet, running at different shaft angles and different depths.” Because of this variety, PowerTech manufactures more than 100 different propeller variations for V-6 outboards.
The driving force behind outboard prop technology wasn’t top-secret Navy data, but tighter emissions requirements that spawned more four-stroke outboards. Heavier engines made boats harder to keep on plane. Four-strokes distributed horsepower differently across rpm and were geared to turn propellers slower. Quieter motors demanded quieter propellers.
“Now with smaller-displacement engines producing more horsepower, it’s even more important to match the prop, motor and boat,” Powers says. The right props best utilize specific engine technology, like variable valve timing or superchargers.

Powers says boats with handling issues are often simple cases of improper propping. Porpoising, for example, is usually mitigated by adding blade surface area and reducing rake. Falling off plane on hard turns, caused when props ventilate (draw in air) is often resolved by changing the blade shape. Less propeller pitch, more blade surface and less rake usually help boats stay on plane at slower speeds. Adjusting blade diameter, number of blades, surface area and rake can also increase fuel economy.
With the exception of pure racing machines, sterndrive boats tend to all be similar, and so are their props. Sometimes a bit of cruise economy can come at the expense of top-end speed, but unless a boat exhibits a specific problem, Powers doesn’t typically see enough gain to justify new props for sterndrives.
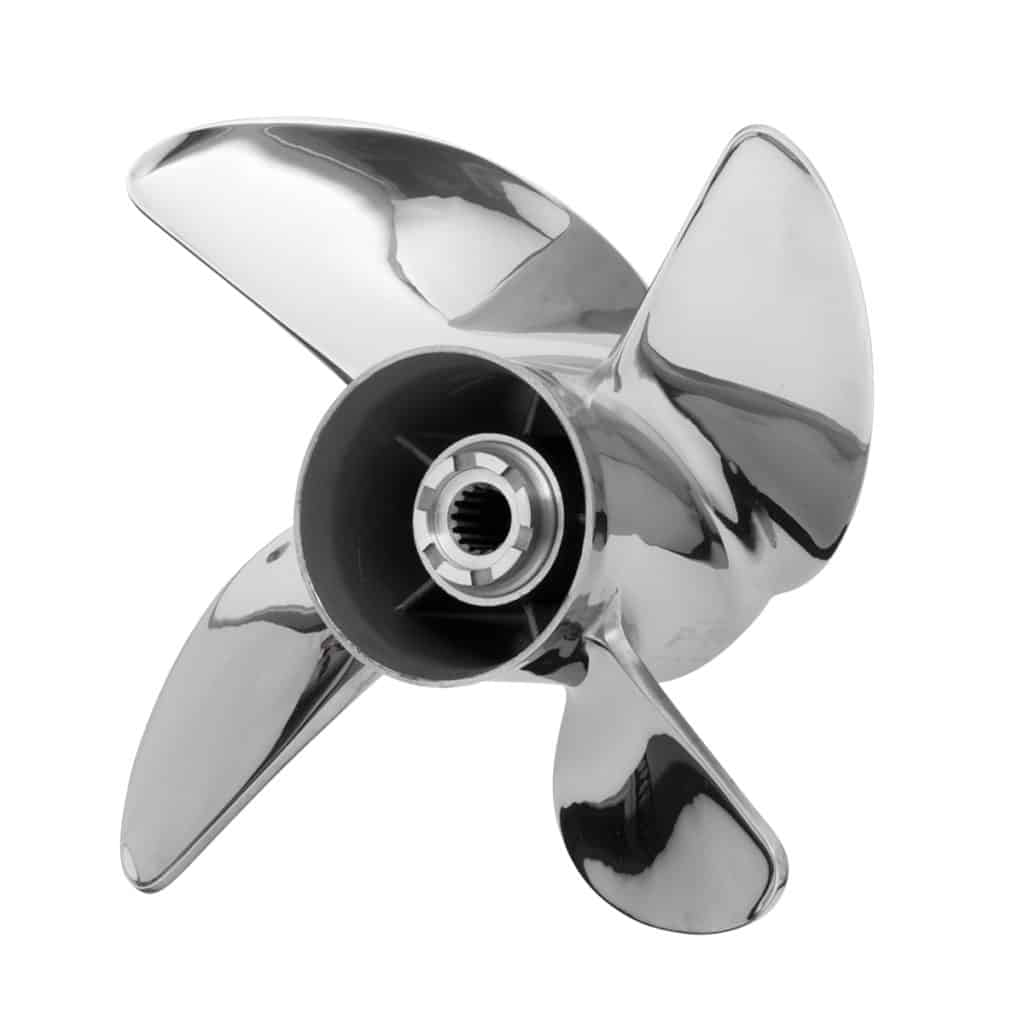
Availability and Cost
“At first, we were designing completely custom props for a series of production boats,” Mitchell says of monthslong projects to aid builders in hitting performance targets. Based on those experiences, Michigan Wheel Marine developed automated tools to design semicustom propellers quickly and inexpensively, as well as advanced CNC machining to produce those complex shapes. “This makes sophisticated propellers much more affordable, and performance is much more consistent,” Mitchell says. Where propellers previously might require one or two sea trials with tweaks to find perfection, even on production boats, CNC-machined props typically reach rated rpm and match port and starboard engine load at every rpm the first time a boat is launched.
New propeller technology is available off the shelf too. For around 30 percent more than venerable flat-pitch Dyna-Quads, new EQY props with airfoil-shaped blades work particularly well on diesel-powered boats over 40 feet that cruise between 30 and 35 knots [34.5 and 40.2 mph], Mitchell says. Going a little lower tech, many express cruisers in the 30-foot range have three-blade Dyna-Jet or four-blade Dyna-Quad props. For about 10 percent more money than those props cost today, the company’s new DQX series is not a foil shape, but it’s optimized for higher horsepower and newer propeller materials and manufacturing. “Switching from three-blade to four-blade might trade a little top-end speed, but you gain significant efficiency at cruise and smoother operation,” he says.

Maybe Your Current Props Are Wrong
“Sometimes props have been reconditioned so many times, they’re not even the right size anymore, or the boat had the wrong prop design to begin with,” Mitchell says. Boats gain weight as equipment is added, and props are altered with the sole goal of hitting proper full-throttle engine rpm. “Getting the right design and size for the boat can create a huge difference,” he says. Propeller manufacturers can often provide exact parameters to shops with new electronic scanners, like Prop Scan or Hale MRI, so they can reproduce the original prop shape.
And increasing accuracy of repairs might solve propeller problems. “MRI ensures tighter tolerances,” Harrison says. “It also ensures the geometry is the same on each blade,” which is particularly important to reduce vibration. Improving Class 1 or Class 2 repair tolerance propellers to the highest Class S, while tweaking pitch and cup at the same time to better match a boat’s needs, costs about $550 for a 21-inch, four-blade, cupped prop — versus $400 per prop for an ordinary Class 1 or Class 2 repair. This alone can wring more efficiency and reduce vibration from existing propellers.
So how did the Navy’s top-secret propeller design technology land on production-boat prop shafts? “The Navy moved to different technology,” Platzer says, but he won’t elaborate. Stay tuned. Boating could be reporting on ultraquiet, super-efficient, vibration-free Caterpillar drives next.

Sea-Trial Guide For Propeller Buyers
Thinking of new propellers? For optimum propping, provide the prop shop with data based on the boat’s performance as currently propped. To gather this, start with a clean bottom, normal load and half-full fuel tanks. At each 400 rpm for gas or 200 rpm for diesel (recorded twice, on reciprocal compass headings), note speed and running angle (buy an inexpensive clinometer), plus electronic engine load and/or fuel consumption (exhaust gas temperature is ideal on mechanically governed diesels). Use one tab/engine trim setting through all rpm; if the boat requires multiple trim settings, note what they are at each rpm. Record wind, sea and current, and mention anything that changed the boat’s windage, weight or balance from original — hardtop, extra generator aft, all-chain anchor rode, etc.