
Look up boarding ladders in a marine catalog and you’ll find a bewildering array of models, some made from stainless steel, others from aluminum.
The choice in metals is not limited to boarding ladders. A wide range of boat accessories come in either aluminum or stainless steel, including window frames, rod holders, grab rails, drink holders, table and seat pedestals, and more.
In addition, you might need to decide between aluminum and stainless for a custom-built T-top or wakeboard tower. How do you choose? Jose Chao, strategic product category manager for Taco Marine, offers these tips.
Aluminum Highs and Lows
“Aluminum excels where there is a need for high strength-to-weight ratio,” says Chao.
Aluminum weighs 66 percent less than stainless steel, which can be critical if you’re keeping weight to a minimum. Aluminum also tends to be less expensive than stainless, Chao adds.
Most T-tops, hardtops and towers are made from aluminum to help minimize weight aloft and help keep the center of gravity as low as possible.
On the downside, aluminum is a soft metal that can scratch or ding easily. Once the surface is broken, it is subject to ongoing corrosion that creates a white, crusty appearance that will spread out from the damaged area, Chao points out. This process tends to accelerate in a saltwater environment.
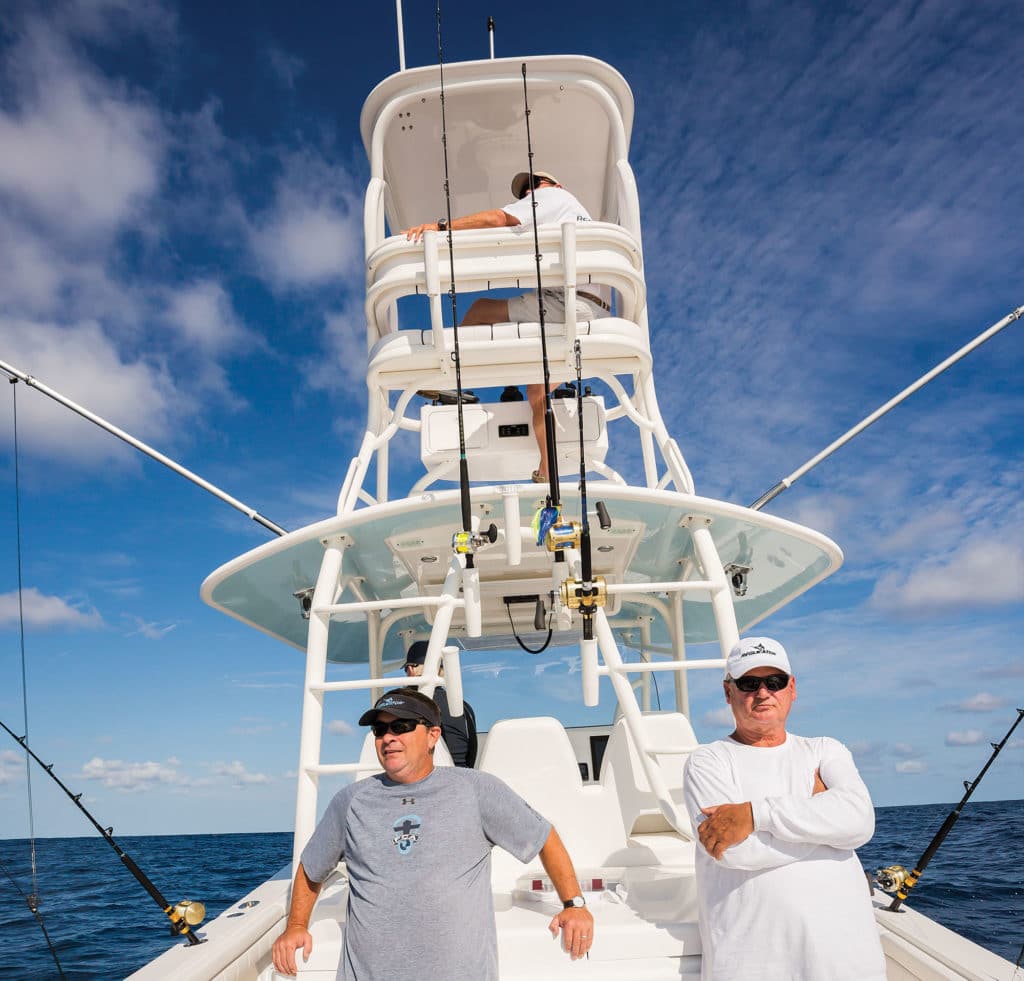
Stainless-Steel Highs and Lows
Stainless steel excels where there’s a need for greater strength, Chao advises, especially where you want a metal that resists bending. This includes deck hardware, seat hardware and anchor rollers, he says. Stainless also resists scratches and dings better than aluminum.
On the other hand, stainless is more expensive, and as indicated earlier, it’s three times heavier than aluminum. When used for structures such as hardtop frames, it not only adds weight aloft, but it can also create stress, resulting in fiberglass fractures over time. To prevent this, reinforce the fiberglass at support points, says Chao.
Grades of Aluminum
The best grades of aluminum for marine applications include 5000 and 6000 series alloys, Chao says. Alloys typically used for sheet and plate aluminum include 5052 and 5086, which offer high strength and corrosion resistance; 6061 and 6063 alloys are often used in extrusions; and 6463 finds applications in tops, towers, rails and leaning posts. (See “Marine Metals” for more on aluminum alloys.)

Grades of Stainless Steel
Commodity-grade stainless steel is 304, but look for 316-grade stainless for marine accessories. It contains molybdenum and more nickel for greater strength and corrosion resistance, and thus is preferred for most marine applications. (See “Marine Metals” for more on stainless alloys.)
Finishes
Make sure the stainless in the accessory features a polished finish, which allows the chromium in the alloy to react with oxygen in the air to form an invisible chrome-oxide surface layer to maximize corrosion resistance. If surface corrosion happens to appear in the future, it is relatively easy to polish out.
Aluminum, on the other hand, needs more than polishing to resist corrosion. Make sure it is either anodized or powder-coated. With anodizing, parts are dipped in a chemical bath that essentially oxidizes the surface, but with an esthetically pleasing texture and sheen.
Powder-coating is growing in popularity, says Chao. This is applied in ovens where a spray coating of powder is heated to melt and chemically bond to the metal surface. Powder-coating is easier to touch up and repair than anodized aluminum, says Chao.

Marine Metals
Aluminum Alloys (content percentages)
5052: aluminum 95.7 to 97.7, chromium 0.15 to 0.35, copper 0.1, magnesium 2.2 to 2.8, manganese 0.1, silicon 0.25, zinc 0.1
5086: aluminum 93 to 96.3, chromium 0.05 to 0.25, copper 0.1, magnesium 3.5 to 4.5, manganese 0.2 to 0.7, silicon 0.4, zinc 0.25
6061: aluminum 96 to 97.4, chromium 0.04 to 0.35, copper 0.15 to 0.4, iron 0.7, magnesium 0.8 to 1.2, manganese 0.15, silicon 0.4 to 0.8, titanium 0.15, zinc 0.25
6063: aluminum 87.1 to 91.4, chromium 0.18 to 0.28, copper 1.2 to 2, magnesium 2.1 to 2.9, manganese 0.3, silicon 0.4, zinc 5.1 to 6.1
6463: aluminum 97.9 to 99.4, copper 0.2, iron 0.15, magnesium 0.45 to 0.9, manganese 0.05, silicon 0.2 to 0.6, zinc 0.05, residuals 0.15
Stainless-Steel Alloys (content percentages)
304: iron 65 to 71, carbon 0.08*, chromium 18 to 20, manganese 2, nickel 8 to 12, nitrogen 0.1, phosphorus 0.045, silicon 0.75, sulphur 0.03
316: iron 62 to 69, carbon 0.08*, chromium 16 to 18, manganese 2, molybdenum 2 to 3, nickel 10 to 14, nitrogen 0.1, phosphorus 0.045, silicon 0.75, sulphur 0.03
*304L and 316L contain 0.03 percent carbon